Overall Equipment Effectiveness (OEE) is a crucial metric for evaluating the efficiency and productivity of your manufacturing processes. By understanding and optimizing OEE, you can identify areas for improvement in your production line, ultimately leading to improved worksite efficiency and budget optimizations.
What is Overall Equipment Effectiveness? (OEE)
OEE provides insight into how well your equipment and processes function, enabling you to identify areas for improvement and optimize production efficiency. OEE considers three primary factors: availability, performance, and quality.
Equipment Availability
This factor measures the percentage of scheduled production time that your equipment is operating. Downtime due to breakdowns, maintenance, or lack of use, are all factors that can significantly impact components of OEE.
To calculate availability:
- Determine the total planned production time (excluding scheduled breaks).
- Subtract any unplanned downtime from the total planned production time.
- Divide the result by the total planned production time.
Equipment Performance
Performance refers to the speed at which your equipment operates compared to its maximum potential output. Factors such as slow cycles or minor stoppages can lead to low-performance scores in OEE calculations.
To calculate performance:
- Determine the ideal cycle time for each product being produced on your line (time required for one unit at maximum capacity).
- Multiply this value by the number of units produced during operational hours.
- Add up all of these values across different products in your line.
- Divide this sum by the actual operating hours.
Quality
The quality component evaluates the number of products produced without defects during production. A high-quality score indicates that most products meet specifications and require minimal rework or scrap.
To calculate quality:
- Determine the total number of good units produced (without defects).
- Divide this value by the total number of units produced (both good and defective).
To calculate OEE, multiply these three components: Availability x Performance x Quality = OEE.
By analyzing each aspect individually, you gain valuable insights into where you can improve your industrial worksite — reducing downtime, increasing throughput speeds, or improving product quality.
What is a “good” OEE rating?
An OEE of 85% or greater is considered to be a good OEE rating. On average, most companies have an OEE of 60%. A poor OEE rating is considered to be 45% or less.
What is the Difference Between OEE and Efficiency?
OEE is a measure of manufacturing performance that takes into account all aspects of production, including equipment availability, performance, and quality.
It is a comprehensive metric used to measure the efficiency of equipment by calculating how much actual output is produced relative to its potential.
Efficiency, on the other hand, is a measure of how effectively resources are used to produce a given outcome. It is calculated by dividing the output of an activity by its total inputs. While OEE takes into account all aspects of production, efficiency focuses solely on resource utilization and does not consider factors such as quality or defects.
OEE is a more comprehensive measure than efficiency because it considers all the components of production.
The Importance of Monitoring Low OEE Scores
A low OEE could signify inefficiencies within your manufacturing operation that could be costing you both time and money. Regularly monitoring these scores enables you to pinpoint specific issues affecting productivity levels so they can be addressed promptly before further losses occur.
Six common big losses in lean manufacturing are:
- Equipment failure: Unexpected machinery breakdowns that lead to production loss.
- Setup and adjustments: The time spent reconfiguring equipment for different products or tasks.
- Idling and minor stoppages: Delays due to small issues such as tool changes, material availability, etc.
- Reduced speed: Slower-than-normal production speeds due to inefficient processes.
- Process defects: Defective materials, parts, or products that are rendered useless.
- Reduced Yield: Lower-than-expected yields due to subpar performance or quality.
By leveraging the Spot-r IIoT platform, you can easily track and analyze OEE data in real-time, allowing for swift identification of potential problems and informed decision-making to optimize your production line.
Which Industries Benefit From OEE?
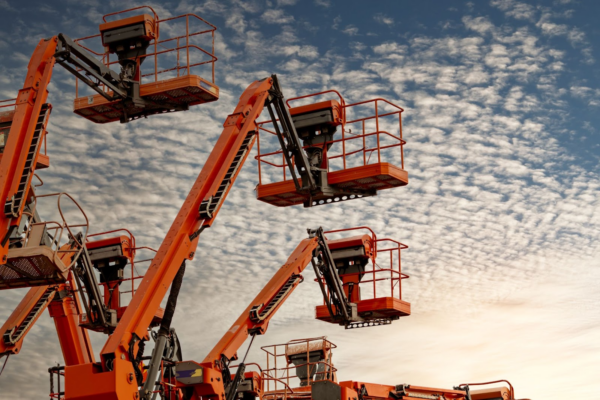
By implementing OEE, businesses can identify areas of improvement and make informed decisions to enhance their operations.
Here are some key industries that benefit significantly from utilizing overall equipment effectiveness software:
Process Manufacturing
IIoT in the chemical, oil, and gas industries can help manage production and ensure safety. OEE enables companies to track and measure plant performance, reduce costs associated with wasted resources, and improve efficiency overall.
Power and Energy
Energy IoT solutions offer the opportunity for businesses to generate more power, reduce wastage and optimize operations. OEE helps companies track equipment performance and identify potential issues so they can be addressed quickly.
Construction
Construction safety management software focuses on making sure that construction sites are safe and secure. OEE helps businesses identify any areas of concern so they can take proactive steps to improve safety standards.
Mining
Mining IIoT solutions can help businesses reduce costs and improve safety measures. OEE helps companies track equipment performance and identify any areas of concern so they can take steps to optimize operations.
6 Advantages of Implementing OEE Tracking on Your Industrial Worksite

By understanding the advantages of OEE, you can make informed decisions about how to optimize your operations and achieve greater success:
1. Enhanced Productivity
OEE helps identify inefficiencies within production lines by measuring availability, performance, and quality metrics. This information allows you to pinpoint areas for improvement and implement changes that will boost productivity levels across your entire operation. With accurate OEE calculations, you’ll be able to track progress over time and ensure continuous growth.
2. Reduced Costs
An optimized production line with a high OEE score is more likely to operate at lower costs due to minimized downtime, fewer defects or rework requirements, and better utilization of resources such as labor and materials.
As a result, companies implementing effective OEE strategies often experience significant cost savings without sacrificing product quality.
3. Improved Quality Control
A higher quality score indicates less waste generation through defective products or reworks required post-production.
4. Early Detection of Issues
By monitoring OEE in real-time, you can identify potential issues before they escalate into more significant problems that could lead to costly downtime or damage your reputation.
5. Data-Driven Decision-Making
OEE data provides valuable insights into how well your equipment performs relative to its potential capacity. By analyzing this information, you can make informed decisions about where to invest resources, such as maintenance efforts or new machinery, to optimize productivity levels.
A robust OEE calculation process will enable you to track trends over time and ensure continuous improvement across all aspects of your operation.
6. Easier Evaluation of ROI
OEE data can help you determine the return on investment (ROI) for any changes made within a production line, allowing management teams to justify expenses based on quantifiable results rather than relying solely on intuition or anecdotal evidence.
This approach leads to smarter investments that drive long-term growth and success within an organization.
Simplify OEE Implementation with Triax
At Triax Technologies, we aim to simplify OEE optimization with:
- Data-driven insights: Our IIoT platform provides real-time analytics that allows you to quickly identify trends in low OEE scores so that you can take corrective actions.
- Benchmarking: Comparing your facility’s performance against industry standards is crucial when aiming for continuous improvement. The Spot-R IIoT platform enables easy benchmark comparisons so that informed decisions can be made regarding optimization strategies.
- Actionable recommendations: Our team will provide actionable recommendations for improving your OEE score and overall worksite performance.
We understand that every industrial worksite is unique, which is why we offer personalized support throughout the implementation process. Our team of experts will work closely with you to ensure a smooth transition while providing guidance on best practices for maximizing OEE scores in your specific industry.
Book a demo and see how Triax can help you today.