Digital innovation has truly transformed how plants and refineries keep their workers safe.
Let us show you why smarter digitization is the linchpin to safer, more efficient process manufacturing sites – and innovative ways to leverage this technology yourself.
The Current State of Plant & Refinery Worksite Safety
On-site injuries and fatalities – both contractor-related and company-related – are rising:
- The rate of reported injuries on job sites increased by 10% from 2020 to 2021, accounting for 580 lost work day cases
- Of the total injuries reported, 20% were categorized as slips and falls
- 18% were categorized as “being struck by”
The future of plant safety relies on a fully-integrated refinery operation management system that improves on-site visibility for managers, improves safety, and facilities faster emergency response times.
5 Ways to Improve Worksite Safety Protocols
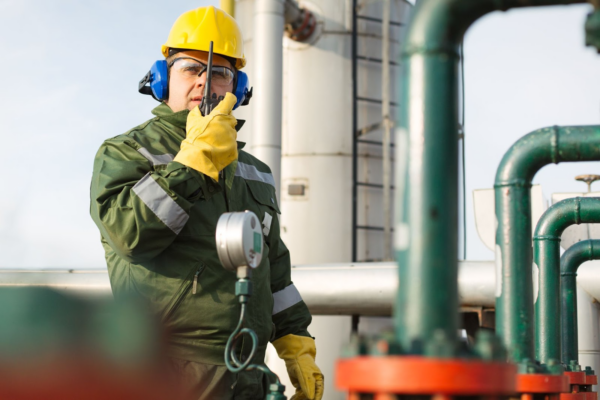
For plants and refineries, improving worksite visibility and implementing automation are the two ways they drive the most impact across all operations.
So how do they do these two things?
They leverage Industrial Internet of Things (IIoT) software for the chemical, oil, and gas industries to become proactive rather than reactive about their worker safety and on-site hazards.
Let’s take a look at five specific IIoT technologies and features that are transforming industrial worksites today.
1. Real-Time Hazardous Area Monitoring and Geo-Zoning
Monitoring hazardous areas in your worksite can be difficult and time-consuming.
Real-time monitoring lets managers know the moment an unauthorized person enters a specific zone or gets near a piece of equipment. Managers can proactively alert a worker of the hazards in the zone and automatically deny access, mitigating future injury risks.
Wearable devices that sync to one central dashboard can help you keep a pulse on where workers, equipment, and large machinery are on a given site, at any time.
When considering this technology, it’s important that your refinery only looks for solutions and tools rated for Intrinsically Safe worksites, which is the engineering control for the most hazardous worksite.
2. Instant Accident Detection
Response time is critical when an accident happens on a worksite.
IIoT digital innovation in the chemical, oil, and gas industries reduces it to zero with fall-detection sensors and automatic alerts built into on-site worker wearables.
Without connected worker software in place, individual workers must rely on someone witnessing or hearing the incident – or on their own ability to call into management. This poses an even bigger problem for lone workers, noisy environments, and remote worksites with no cell service.
Digital innovation in the chemical, oil, and gas industries means managers can closely monitor areas where past injuries have occurred, implementing additional safety notices and protocols for workers. It also allows for a seamless transfer of worker location to first responders if and when an accident does occur.
3. Automatic Evacuation and Muster Activation
The best time to prepare for accidents and emergencies within a refinery is before they happen.
And, similar to the above example of an individual injured person, when a larger-scale accident or risk arises, it’s imperative to have an effective emergency evacuation plan in place.
One that you already know works.
You might be surprised to know that the same digital innovation in the chemical, oil, and gas industries that monitors equipment utilization and helps improve labor productivity, can also serve as an extremely effective emergency management software that helps companies meet and exceed OSHA emergency response requirement standards.
4. Customizable Access Control Alerts
Create restricted zones as well as zone and equipment-specific alerts in your IIoT software.
While one of the benefits of digitization is that most features are automatic and instantaneous. Great digital innovation is also highly customizable.
Refineries can use their own criteria to manage and monitor every aspect of their worksite, giving managers better oversight of operations and safety protocols.
For example, if your worksite has areas that are more dangerous than others, you can require restricted access or use real-time location tracking in place of manual worker check-ins.
The best IIoT safety software for refineries will allow two-way communication within their alert system as well. This helps put the safety of each individual in their own hands, with constant, reliable communication channels to offsite management.
5. Lone Worker Safety
Lone workers pose a significant risk in and near refineries.
Proper training, real-time monitoring, and two-way communication (not reliant on cell service) are three ways to decrease this risk, though it’s impossible to eliminate it completely.
Having a reliable, automated system in place that decreases emergency response times and helps first responders locate individuals is one of the best ways to reduce lone worker injuries and fatalities.
Implement Refinery Digitization with IIoT for a Safer Worksite Today
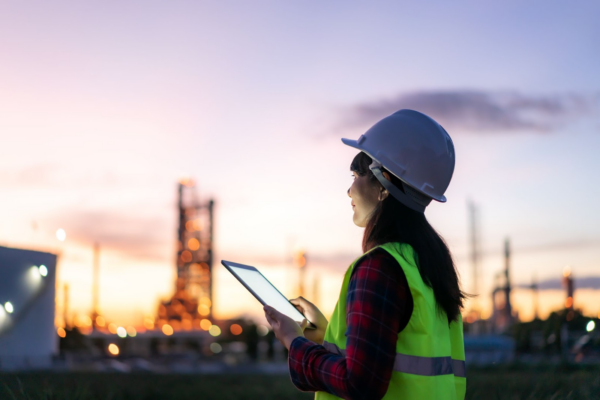
One thing is clear: the impact and importance of digitization in the chemical, oil, and gas industries cannot be overstated.
When considering how to digitize your refinery, it’s crucial to select a comprehensive IIoT solution that brings all your data into one centralized place, offering unparalleled access and visibility to worker-level data and insights.
Because for dangerous worksites, visibility means safety.
We’ve seen refineries effectively use these five tips to keep their workers safe each shift, flattening or even reversing the most recent injury and fatality statistics.
In fact, after implementing the Spot-r IIoT solutions by Triax, companies have reported up to a 72% improvement in evacuation times and up to a 91% improvement in emergency response times. One company was even able to use two-way alerts, automatic location detection, and automatic emergency protocols to locate a lone worker in just 10 minutes.
Book a demo to learn more about the Triax features that are leading digital innovations in the chemical, oil, and gas industries.