More than 30% of all turnarounds experience significant scheduling delays. This can cost businesses millions of dollars and can delay the completion of the turnaround.
However, when organizations implement tools and solutions that help site managers gain greater worksite visibility, these scheduling delays can be avoided. We’ll discuss actionable strategies to improve turnaround management in your organization. We’ll also discuss how IoT solutions can drastically reduce turnaround times and save your organization millions of dollars in turnaround costs.
What is a Turnaround?
A turnaround on an industrial site refers to a planned and scheduled event where operations are temporarily halted or minimized to conduct maintenance, repairs, upgrades, and inspections.
Turnarounds are typically conducted at regular intervals or when specific events, such as the expiration of equipment warranties or the need to comply with regulatory requirements, occur. The duration of a turnaround can range from a few days to several weeks or months, depending on the scale and scope of the turnaround activities.
Common Challenges in Turnaround Management
Industrial turnarounds are a complex process involving hundreds of contract workers and numerous equipment assets at a facility. Since these facilities are so large, site managers often have little visibility into all workers and equipment present at any given moment. This lack of complete worksite visibility makes it more difficult for site managers to coordinate all of the moving parts of a turnaround.
Not only does low visibility make it difficult for site managers to manage turnarounds but it also can create potential safety hazards. For example, if a worker is injured on the job, and site managers aren’t immediately made aware of it, it will take longer for them to locate the worker and send first responders. IIoT Solutions are key to improving turnaround management, as well as the implementation of other important strategies.
Strategies to Improve Turnaround Management & Planning
Improving turnaround management comes down to focusing on three primary areas: pre-turnaround planning, risk assessment, and safety planning. IoT solutions can help you automate many processes associated with these tasks.
1. Set Clear Objectives & Allocate Resources
During pre-turnaround planning, you’ll need to define specific goals and outcomes you aim to achieve during the turnaround. Efficient pre-turnaround planning can help identify potential logistical pinch points.
For example, one petrochemical contractor was hoping to increase the speed of their turnaround efforts, so during pre-turnaround planning they analyzed what was causing a lack of productivity within their workforce. They found that workers had long wait times in the toolroom, signing in and out of the control room, and getting on to the job site at the beginning of their shift. They adopted an IoT solution that helped them automate shift check-ins, and stagger shift start times to improve sitewide efficiency.
From there, you’ll determine the necessary resources required for the turnaround, including personnel, equipment, materials, and external contractors. You’ll need to ensure that you’re allocating resources effectively, considering factors such as availability, cost, expertise, and compatibility with project requirements.
2. Set Budgets and Estimate Costs
80% of turnarounds end up going over budget by at least 10%. To control costs, developing a comprehensive budget that covers all aspects of the turnaround, including labor, materials, equipment rental, and contractor fees is essential. You’ll want to consider potential cost overruns and incorporate contingency funds to handle unexpected issues.
3. Optimize Scheduling and Coordination
Once you’ve established your budgets, you’ll then develop a detailed schedule that breaks down the turnaround into manageable tasks. Coordinate activities among different teams, contractors, and suppliers to ensure smooth execution. Adopting an IoT solution that allows for greater site visibility will help you monitor progress regularly and adjust the schedule as needed to minimize delays.
4. Implement IoT Technology for Greater Site Visibility
To improve turnaround management you need to have full site visibility into equipment, workers, and contractors. On large industrial worksites, it’s nearly impossible to accomplish this without implementing sitewide visibility solutions.
Spot-r IoT software is a comprehensive solution that combines wearable safety technology, AI-powered computer vision cameras, and cloud-based data analytics to capture decision-grade data from your site in almost real time. Contractors and workers can wear the Spot-r device, and you’ll get access to an easy-to-use dashboard that displays all worker locations, so you can validate where your workforce is at all times.
5. Conduct a Risk Assessment
To keep workers safe and minimize delays, you should conduct a comprehensive risk assessment to identify potential hazards, safety concerns, and operational risks. IoT technology such as Spot-r can help you conduct an effective risk assessment. For example, Spot-r can identify how many workers are in a specific workzone or area, and if restricted areas are easily accessible to non-authorized personnel.
Once you’ve identified all potential risks, you should then develop risk mitigation strategies and contingency plans to address these issues. For example, establishing a mustering point for contractors in the event of an emergency. You should also ensure that all workers are trained in safety protocols and adhere to strict safety measures throughout the turnaround.
6. Analyze Worker Productivity
Effective turnaround management requires optimizing worker productivity on industrial work sites. To optimize and improve labor productivity, you should first get a clear understanding of your workforce’s productivity by looking at key metrics such as time on tools, amount of work completed, and labor efficiency variance.
To do this effectively, you need to have this data readily available. An IoT solution such as Spot-r collects data from computer vision cameras, then aggregates worker productivity data into one user-friendly dashboard. Spot-r then provides personalized recommendations for improving labor productivity and efficiency using AI.
For example, Spot-r can tell you where the turnaround workforce is spending their time and can help measure a contractor or crew’s zone productivity benchmarks. Spot-r can also tell you how long workers are spending in each zone, and help you improve your time on tools metrics. By analyzing labor productivity data and making changes to your processes based on that data, your organization can save valuable time and significant cost savings on turnarounds. Additionally, by using Spot-r, contractors on turnaround projects consistently operate at around 50% time-on-tools.
7. Adopt Equipment Monitoring Solutions
Industrial facilities have hundreds, if not thousands, of equipment assets. It’s incredibly difficult to keep track of equipment maintenance needs and measure utilization for every single piece of equipment on a job site without a large workforce. IoT solutions such as Spot-r can provide site managers with advanced equipment metrics such as real-time usage, downtime, OEE, and efficiency in one user-friendly dashboard.
With Spot-r, you can simply attach the in-field device to each piece of equipment, and you’ll get instant access to all important equipment metrics in your dashboard. Spot-r can also help you predict and prevent future equipment downtimes so you can improve turnaround management and pre-turnaround planning.
Additionally, organizations are often overbilled by their equipment rental partner for underutilized equipment by 20% or more, leading to unnecessarily high equipment costs. Adopting an equipment monitoring solution such as Spot-r will ensure that every piece of equipment is accounted for and that any underutilized equipment can be removed from the premises. This helps organizations save millions of dollars on underutilized equipment and helps ensure equipment efficiency.
Spot-r IoT Solutions Can Significantly Improve Turnaround Management
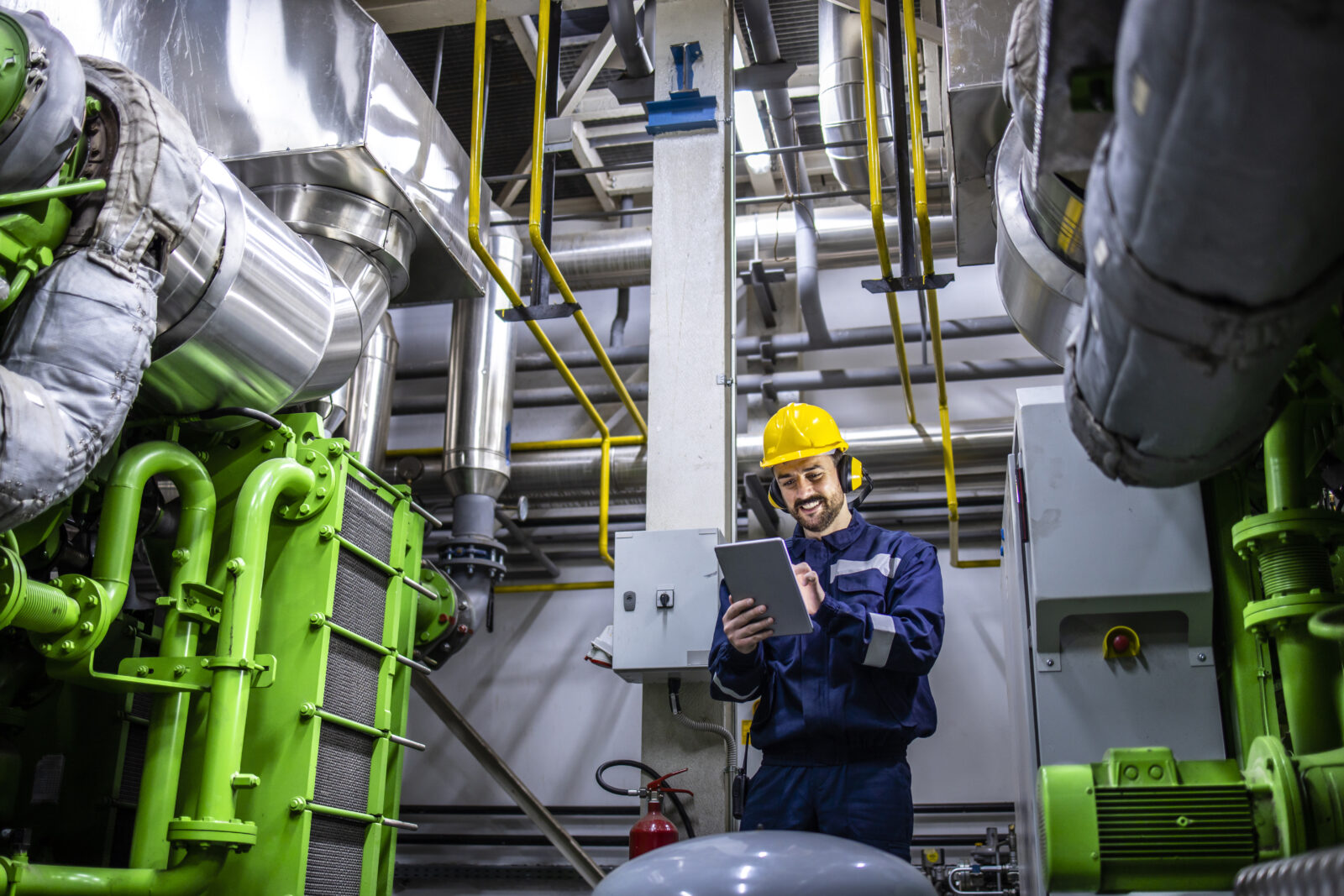
Energy, manufacturing, construction, and large industrial facilities can save valuable time and millions of dollars in turnaround costs by setting effective budgets, allocating resources properly, setting measurable goals, and gathering data on equipment and worker resources using IoT solutions.
Implementing IoT solutions such as Spot-r can help your organization improve turnaround management. For example, one Fortune 500 Fertilizer and Chemical company didn’t have full visibility into where productivity bottlenecks were occurring on the worksite during turnarounds and was unable to obtain accurate employee headcounts.
Implementing Spot-r helped them gain greater visibility into productivity bottlenecks, resolve those bottlenecks, and achieve six-figure savings on their turnaround project. Take a look at this case study to see the full results.
Ready to see how Spot-r can help your organization improve turnaround management? Request a demo of Spot-r to see how.