The continuous search for improved work site efficiency and safety has led to the emergence of new solutions and calls for better digitization of industrial worksites.
Digital twin IoT technology is an example of one such solution, lending itself to myriad benefits on worksites. So let’s explore the intersection between digital twins and IIoT on industrial sites – and explain why that matters to you.
What is the Industrial Internet of Things (IIoT)?
The Internet of Things refers to an ever-growing network of internet-capable devices that can communicate with each other. Smartwatches, fitness trackers, smart speakers, smart doorbells, thermostats, and pacemakers are all examples of commonly-used IoT devices.
Industrial Internet of Things (IIoT) refers specifically to IoT solutions for companies in industries such as process manufacturing, heavy manufacturing, construction, and mining. IIoT is developed to enhance onsite processes, leading to improved labor productivity, equipment utilization, and safety protocols.
And the rapid advancement of IIoT technology has resulted in the exponential increase of another revolution: the digital twin technology.
What is a Digital Twin in IIoT?
Put simply, a digital twin is a digital representation of a physical object or a system, allowing for virtual simulations before being implemented in the real world. Digital twins can include buildings, factories, outdoor worksites, equipment, workflows, and even people.
For industrial worksites, an example of a digital twin would be one that replicates an entire production system or all the assets on a given work site.
A Brief History of Digital Twins
The term “digital twin” was coined at NASA in 2010, though it is said to have unofficially been used since the 1960’s to replicate, study, and perfect space missions before sending astronauts out on spacecraft.
The concept of digital twin and IIoT technology was officially applied in the manufacturing industry in 2002.
Creating a digital twin is a complex process that requires applied mathematics to replicate the workings of an object or system in a digital environment. But it presents the huge benefit of having a working, testable, small-scale prototype of something before spending millions of dollars to design, build, or manufacture the physical item or system.
IBM places digital twin technology output in one of four categories based on the extent of product magnification:
- Component twins or part twins are a digital representation of how a component or the smallest functioning unit of a machine works.
- Asset twins represent how components work together.
- System twins or unit twins show how assets combine to form a functioning system, such as a production line.
- Process systems twins show how systems work together in a factory, for instance.
Digital Twin vs IIoT
Digital twins and IIoT are different but complementary technologies.
Digital twins are virtual environments where you can run multiple simulations. You can use real-time data from a physical system to keep track of the performance, safety, or efficiency of the system.
They are models of complex things that do or will exist in the physical world.
Meanwhile, engineers use data collected from IIoT devices to develop digital twins.
IIoT and Digital Twin Applications for Different Industries
To understand this, we need to explore applications of digital twin and IIoT software in different industries – as well as some digital twin use cases.
Digital Twins in Field Service Management and Enterprise Asset Management
Digital twin technology has the ability to bring together field service management (FSM) and enterprise asset management (EAM). By being able to map out the entirety of their assets, companies can predict asset failures and plan their operations better.
For example, companies can run simulations to determine where to build a site warehouse within a big field for maximum efficiency. They can also come up with contingency plans for emergencies that require evacuation, by simulating different situations and finding a process that yields the best safety outcomes.
This results in complex, accurate, and completely automated emergency management solutions.
Digital Twins in Manufacturing
The significance of data in manufacturing processes begins right at the conception of a new idea and extends the entire lifespan of the finished product.
Designers of new products can make digital twins and run tests on them as proof of concept. During production, data from IIoT sensors can reveal faults in the length, thickness, or strength of the material. The monitoring continues well after the finished product goes out for use. When a product such as a jet aircraft is in use, data from IIoT devices can inform engineers to alter the designs of future models to improve performance.
A case study from Deloitte details how an industrial manufacturer used digital twins and IoT data to identify faults in their production process.
The insights resulted in a 15-20% reduction in rework.
Products and processes that are very complex, expensive, or that carry a risk of high variability in their manufacturing processes are great digital twin candidates. Making a digital twin prototype means that you can identify costly faults very early on.
Digital Twin Technology in the Construction Sector
Construction sites are leveraging digital twin and IIoT technology to increase efficiency in their projects.
For example, digital twins can be used to predict precise labor and material costs. This not only prevents the inflation of project costs, but it enables better projection of supply chain needs.
Engineers can overlay digital twins in the field using Augmented Reality (AR) technology to inspect buildings for quality. In case of errors in the field, engineers can mark them on the digital twin and figure out workarounds, enabling them to solve specific problems without stalling entire projects.
Digital twin models can also greatly enhance safety on large job sites. Here are just three ways to do so:
- A digital simulation or walk-through can quickly uncover previously unforeseen risks, allowing management to fix them before they even arise.
- Safety managers can administer contractor and worker safety training using the digital rendering of a factory or building.
- When designing new factories, our digital twin solution could also be used to optimize the layout for better safety and efficiency.
The Benefits of IIoT and Digital Twin Solutions
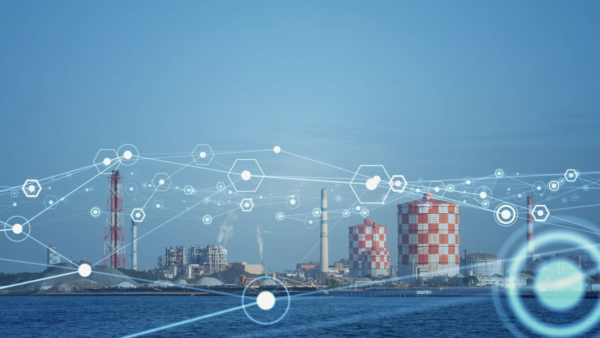
Accelerated product development is one of the most visible benefits of building digital twin solutions. Manufacturers no longer need to build multiple iterations of prototypes. Instead, data from simulations on the original digital twin can be used to build upon subsequent digital twin versions.
Industrial sites that employ digital twin technology to plan the layouts of their factories, worksites, assembly lines, and worker flow can greatly reduce their maintenance costs and improve turnaround efficiency.
Digital twins are also an important digital innovation in the chemical, oil, and gas industries. Energy companies can replicate entire pipelines, oil rigs, and refineries digitally. Data collected by in-field IIoT devices can be synced onto the digital twin. This helps monitor the health of entire operations and carry out predictive maintenance.
Aside from helping predict maintenance needs, digital twins can inform product end-of-life decisions.
Based on accurate data, companies can determine how many hours or production runs a machine can perform. Management can then make informed capital budgeting decisions concerning buying, renting, and replacing machinery, equipment, and more. Specific equipment utilization data from IIoT devices would help decide whether it is feasible to buy instead of lease critical equipment.
The added worker-level visibility and insights gleaned from wearable IIoT devices also unlocks nearly endless automation and on-site optimization possibilities.
For example, workers could automatically clock in and clock out, check out tools, and gain access to restricted areas by scanning their wearables at a specific checkpoint. This can lead to an impressive and nearly-instant boost in on-site labor productivity.
Unlock the Benefits of Digital Twin and IIoT With Spot-r Software
Industrial site efficiency is poised to see a huge uptick in the companies that adopt digital twin and IIoT software.
For industrial companies with big plants and worksites on their balance sheets, equipment utilization, refinery turnarounds times, labor productivity, and emergency response times are important figures on their dashboards.
For most, gaining better worksite visibility and accurate data insights are the linchpin for optimizing their most important metrics.
And IIoT solutions, such as Spot-r ™ software by Triax, have revolutionized how companies define worksite visibility on their field sites. By building digital twins of their worksites, processes, and products, they can optimize the efficiency of complex sites while mitigating the risks and costs of needing to re-iterate the non-digital counterparts.
Triax understands the complexities of big industrial operations.
Our digital twin and IIoT solutions make it easier, more affordable, and safer to test new ideas digitally, helping site managers and management teams identify new efficiency opportunities and improve safety levels. Want to learn how you can embark on digital transformation by leveraging digital twin technology on your worksite? Book a demo to see our solutions in action and speak to a qualified member of our team.